团队负责人:李涤尘
所在学院:机械工程学院
一、团队简介
西安交通大学自1993年开始增材制造(3D打印)技术研究,是国内最早开展增材制造技术研究的单位之一。经过二十年的发展,西安交通大学形成了多种增材制造工艺和装备,建立了以快速制造系统为特色工程应用的研究队伍,产生了以卢秉恒院士为学术带头人的“增材制造”教育部创新团队。
研究团队依托机械制造系统工程国家重点实验室(西安交通大学)开展基础研究,在高分子材料、金属、陶瓷、复合材料、智能材料的增材制造等方面取得进展,多项技术成果处于国内领先、国际先进水平。为推动3D打印技术的产业化,在2000年成立“教育部快速成形制造工程研究中心”(市场经营主体为陕西恒通智能机器有限公司),2007年成立“快速制造国家工程研究中心”(市场经营主体为西安瑞特快速制造工程研究有限公司)。建立了一套支撑产品快速开发的快速制造系统,研制、生产和销售16个型号的激光快速成型设备、快速模具设备及三维检测设备。同时开展快速原型制作、快速模具制造以及逆向工程服务。产品在全国各院校、汽车、电器等企业销售应用十多年,客户近万家。近年协助政府和企业在多个地区成功建立产学研结合的推广基地、快速成形制造服务制造中心。通过企业化运作,目前在全国已建立创新服务平台20多家,创新人才培养基地近10家,为2000多家企业提供新产品创新创意设计及快速制造服务。
通过近二十年的技术研发与推广应用,设备用户遍布医疗、航空航天、汽车、军工、模具、电子电器、造船等行业。此外,还积极拓展国际市场,相关设备销售到印度、俄罗斯、肯尼亚等国家,成为具有国际竞争力的快速成形设备制造单位。2016年工业与信息化部批准在西安成立国家增材制造创新中心,中心联合国内主要科研与产业化优势单位开展共性技术研究和产业化孵化作用。西安交通大学在增材制造方面获得国家科技进步二等奖1项,国家技术发明二等奖3项,省部级一等奖4项,在增材制造领域获得发明专利400余项。
二、团队项目
(1)航空发动机空心涡轮叶片的型芯型壳一体化快速精铸技术
空心涡轮叶片是航空发动机、大型舰艇发动机、重型燃气轮机等核心关键部件,被誉为“皇冠上的明珠”,其制造技术是我国“两机”重大专项核心技术之一,因技术难度大、发展起步晚、国外封锁严等,成为制约航空发动机和燃气轮机提升的技术瓶颈。西安交通大学机械制造系统工程国家重点实验室将3D打印技术和成熟的精密铸造技术融合,发明了航空发动机高温合金叶片型芯型壳一体化的快速精铸技术。该技术可显著提升复杂叶片的制造能力、大幅缩短叶片制造的工艺路线、大幅降低制造对叶片设计的限制,对我国航空发动机制造体系和研制体系能力的提升具有重大的革新意义。目前,在国家项目支持下,研究团队已攻克了该技术的关键难题,形成了完备的技术体系,建成了小批量生产线,具备了服务于我国先进航空发动机创新设计的能力。
航空发动机空心涡轮叶片的快速精铸技术的技术原理如图1所示。以CAD数字数据直接驱动,利用光固化3D技术成形制造高精度复杂内腔的树脂原型,采用凝胶注模方法将陶瓷浆料一次贯注成型,冷冻干燥处理后,烧失树脂原型和烧结陶瓷,经过强化处理后,制备出芯壳一体化陶瓷铸型,在此铸型中浇铸金属,经凝固、脱芯等工序,即可得到高温合金叶片。
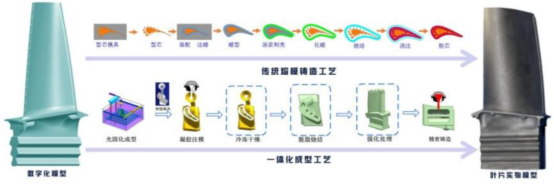
图1-1航空发动机高温合金叶片的快速精铸技术的技术原理
航空发动机涡轮合金叶片的型芯型壳快速精铸技术相比于传统熔模铸造和直接金属3D打印叶片的优势和先进性体现在:成品率高:型芯型壳一体化的原理性优势,精度高、性能好;利润率高:得益于3D打印和成品率较高,周期/成本曲线优异;需求匹配好:精度高、性能好、周期短、成本低。
该技术主要应用:服务于叶片的创新设计。致力于为叶片的创新设计提供全周期,全工况的解决方案;在叶片的论证,选型到最终定型中,可提供:PIV冷态流动树脂模型,叶栅,等轴晶、定向晶乃至单晶叶片;服务于叶片的先进制造。先进冷却结构的一体化铸造成形:采用型芯/型壳一体化快速精铸技术,可实现双层壁冷型芯,气膜孔型芯的直接成型,缩短了加工周期。先进铸造技术:型芯/型壳一体化快速精铸模壳高温性能优异,满足定向晶/单晶航空发动机叶片先进铸造技术的使用要求,目前已实现航空发动机叶片定向凝固制造。该技术还可以用于其它复杂结构零件的制造上,是3D打印与传统铸造技术的结合。
(2)野外环境3D打印维修保障系统
“野外环境3D打印维修保障系统”是针对野外环境条件装备应急抢修所研发的野外修复装备,系统包括零部件数据库软件、三维反求测量系统、金属激光3D打印系统及后处理模块等,其中零部件数据软件具备对零部件的上传、存储、下载、预览等功能,三维反求测量系统具备对破损零部件的扫描、反求、智能解算破损量等功能,金属激光3D打印系统具备对精度要求较高的小型零件进行精确修复和直接成形功能,后处理模块具备对修复完好的零部件进行机加工处理等功能。野外环境3D打印维修保障系统攻克了复杂零部件三维形貌快速扫描测量及建模技术、野外环境下成形过程控形控性技术、缺损模型与待修零件坐标转换技术、系统集成技术等关键技术问题,系统集扫描、反求、修复等功能为一体,具备野外环境条件下对受损装备进行快速修复的功能。
野外环境3D打印维修保障系统可用于野外装备应急抢修、远洋船伴随保障、偏远海岛及高山设备维护、工矿企业装备与模具修复日常维护等。研究成果参加“第二届军民融合发展高科技成果展览”。
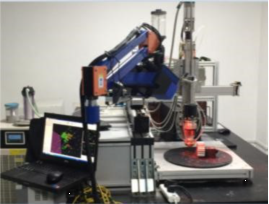
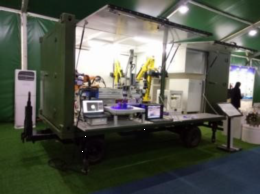
图2-1 3D打印维修样机 图2-2 3D打印系统运输方舱
(3)高性能连续纤维增强复合材料3D打印工艺
本项目以连续纤维增强热塑性聚合物基高性能复合材料零件直接3D打印为目标,采用连续纤维与热塑性聚合物为原材料,利用复合浸渍-熔融沉积的3D打印工艺实现高性能复杂结构复合材料构件的低成本一体化快速制造,打印的复合材料零件的拉伸与弯曲强度分别达到340MPa与390MPa,该技术既改进了传统3D打印零件强度不足的缺点推动了3D打印技术向工业化应用的进程,又克服了传统复合材料成型工艺成本高、周期长的技术瓶颈促进了复合材料在将来的进一步发展与应用,是一次具有革命性的创新与突破。该技术属于国内首创,获得多项自主知识产权,受到国内外越来越多机构的关注,在国内,本项目得到国家重点研发计划、国家自然科学基金、载人航天等项目的支持,开展关于工艺机理与装备等方面的研究,探索该工艺在航空航天领域的应用前景,在国外,分别与德国、俄罗斯等研究单位合作
在当今全球3D打印领域快速发展的形势下,复合材料3D打印具有巨大的发展前景,据SmarTech预测,至2026年全球用于3D打印的复合材料收入将超过5亿美元,未来十年内复合材料将成为3D打印最主要的市场机遇,目前该项技术已经开发出了成熟的工业设备,形成了成熟的装备-材料-工艺体系,具备了商业化应用的条件,已经初步在复合材料轻质结构等方面得到应用,随着该技术的成熟,将来必将在航空航天、汽车交通甚至民用领域得到广泛的应用。
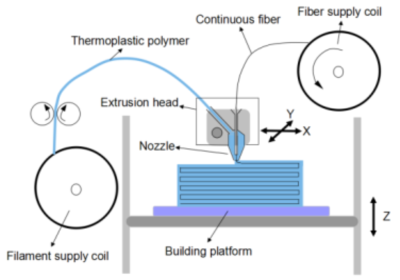
图3-1连续纤维增强复合材料3D打印成形机理
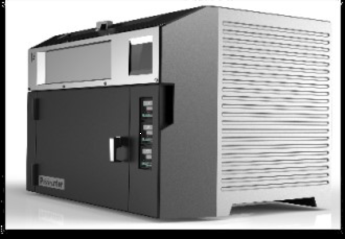
图3-2 3D打印设备
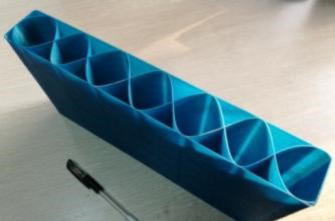
图3-3制作的复合材料零件
(4)陶瓷光固化面成形技术
研制了陶瓷光固化面成形3D打印技术包括自制设备与软件。该设备包涵基本光固化加工模块和多材料光固化加工模块,并有各自独立算法。基本光固化加工模块由运动系统的控制、运动系统与曝光系统的整合、掩膜视频信号与紫外光投影图案的整合等三个部分组成,解决了因不同材料光固化性能的差异引起的成形工艺参数的在线更改、运动加减速导致的曝光时间不稳定、多种投影图案在线调整等难点。
多材料光固化加工模块可调用基本光固化加工模块,但以换槽和清洗、掩膜在线更换功能为主,解决复杂结构模型内部不同材料分层、同层内不同材料的分时成形的问题,为非均质结构和多种光敏材料的一体化成形提供了自动化控制平台。内置分离力测量系统和膜带式加工台,解决了底曝光固化过程中普遍存在的脱层困难的瓶颈问题,并有效地降低层间台阶效应和内部缺陷,提高陶瓷件的外层表面质量和内部结构精度。目前该技术不仅可完成氧化物陶瓷成形,也可用于树脂、光敏水凝胶3D打印成形,具备通过多图案的连续层迭代制造多尺度梯度结构的复合材料支架。该技术可为制造高精度、大尺寸、高强度陶瓷零件提供技术基础。
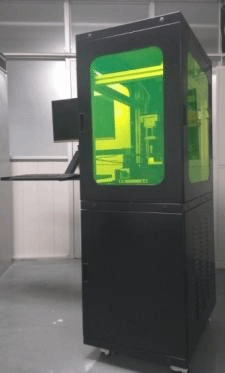
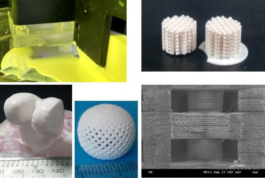
图4-1陶瓷光固化面成形自制设备图4-2成形过程与陶瓷样件
(5)个性化PEEK骨科植入物3D打印技术
对于肿瘤、创伤、疾病等原因造成的骨缺损或骨畸形患者,由于个体性差异大、病患程度不一等原因,传统规范化的医疗植入物经常无法满足要求。因此,本项目采用生物级聚醚醚酮(PEEK)材料作为原料,利用3D打印技术,快速定制个性化、高性能的骨科植入物,从而满足患者切身需求。
相较于传统金属植入物材料而言,PEEK作为一种半结晶高分子材料,具有质量轻,弹性模量接近原骨,减磨耐磨,生物相容性优异和物化稳定性好等优点,成为目前生物假体植入物的理想材料之一。然而,PEEK材料是一种高熔(343℃)、大冷却收缩率、半结晶的热塑性材料,采用传统加工方法,具有材料利用率低、成本高、难以直接成形复杂结构等问题。
本项目团队研发了一种以控性冷沉积为核心技术的3D打印方法以及智能工艺,可以依据应用需求进行力学性能(如韧性、模量)的调控,实现了高性能聚醚醚酮骨科植入物低成本、高精度的控形控性快速制造。相关技术已经完成了世界首例PEEK肋骨临床应用,在国际、国内都处于领先地位。骨科医疗器械行业属于国家重点扶持的鼓励类行业,《医疗器械科技产业“十二五”转向产业规划》等多项政策将骨修复材料、人工关节和脊柱等骨科植入物列为国家重点开发产品。根据多个调查机构的报告显示,骨科植入物市场,尤其是国内骨科植入物市场快速增长态势气势如虹,2015年市场规模达166亿元人民币,超过日本成为全球第二大骨科市场;2012-2015年复合增长率达18%,预计到2019年市场规模将超过300亿元。可以说,骨科植入物市场,尤其是国内市场前景具有极大的发展潜力。而本项目所研发的PEEK个性化骨科植入物3D打印技术,是一种前沿的创新制造方法,将成为骨科植入物市场的新兴热门方向,具有极大的市场前景。
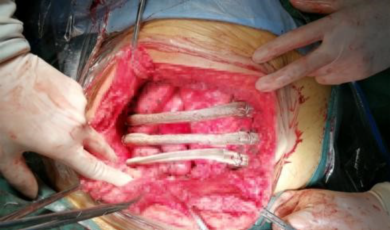
图5-1世界首例3D打印PEEK肋骨临床应用(2017年4月)
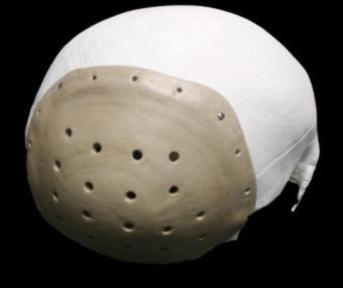
图5-2 PEEK颅骨假体
(6)个性化3D打印医学假体设计软件系统(OrthoDesign)
针对目前3D打印制造个性化人工假体的设计缺乏力学分析依据和标准规范流程问题,该个性化3D打印医学假体设计软件系统,通过整合骨骼建模、假体宏观建模、骨骼/假体装配、优化分析、假体微观建模五个功能模块,实现定制化人工假体智能快速宏观外形设计、假体选型以及内部多孔结构设计。设计后的假体拥有个性化的宏观几何形貌和个性化的内部多孔结构,可直接应用与3D打印制造技术,该结构能够促进假体植入后骨长入能力,提高植入后远期假体稳定性。
内植物设计:提供面向常用内植物的关键几何参数设计方法,通过假体重要特征参数的尺寸缩放,实现假体快速建模;提供内植物模型库,允许用户通过选择不同型号的内植物进行服役性能分析,辅助术前选型规划;亦可通过CT图像重建的方式设计完全定制化的内植物。
假体服役性能分析与优化设计:软件集成了有限元分析模块,针对假体植入后服役性能进行生物力学分析开发了专用工具箱,简化传统假体有限元分析流程;在力学分析与优化中,以内植物植入后强度、早期稳定性和远期稳定性为核心优化准则,通过有限元方法对假体内部弹性模量进行优化,目的是提高假体的骨传导能力,促进假体植入后骨长入。
假体多孔设计:根据力学优化分析结果中梯度模量分布或用户需求自定义,通过对不同类型单元体进行阵列的方式,自动生成局部或整体多孔结构,便于3D打印个性化制造。
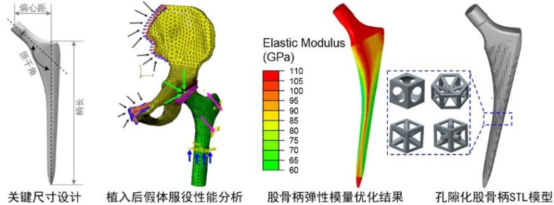
图6-1.个性化3D打印医学假体设计软件系统应用实例:人工髋关节股骨柄
软件可以应用于:人工假体快速敏捷设计平台,解决了医疗器械公司缺乏产品设计依据和送检产品选型的难题;人工假体服役性能便捷评价平台,在兼顾假体常规的安全性、稳定性、强度的基础上考虑了假体植入后骨长入性能的促进对假体植入后远期稳定性的影响。为医疗器械公司和医生开发出更长寿命假体提供优化平台。多孔假体模型的自动构建平台,模型可直接应用与3D打印制造系统,解决了目前最为严峻的医疗器械公司和医生对可3D打印制造的个性化多孔模型的需求。
(7)关节软骨缺损修复3D打印技术
关节是人体的承载组织和运动器官。关节损伤是危害人体运动功能的多发疾病,直接影响人的运动、进而影响生活健康和生活质量。现有金属和惰性陶瓷的人工关节虽已在关节疾病后期的治疗上获得了广泛应用,但因磨损造成的松动而发生失效。临床医学对大面积骨/软骨缺损的再生修复有迫切需求。因此,如何在关节疾病早、中期进行治疗并形成活性关节再生是再生医学的发展的迫切需求、定制化大尺寸骨/软骨支架设计制造成为关节软骨缺损修复、关节组织工程发展面临的重大挑战。
该技术以大尺寸骨/软骨缺损为研究对象,针对关节体内力学和生物学环境需求,围绕多材料与宏微观骨/软骨支架设计制造和功能评价方法的需要,所开发的活性骨和软骨人造组织同步制造和体外评估方法,为发展具有良好力学和生物学功能的人工活性组织关节提供科学基础与工程实现方法。研发了大尺寸骨/软骨支架的仿生结构设计方法。利用该方法,通过研究膝关节力学环境因素对植入物结构的相互作用关系,已发现了关节韧带、半月板、软骨与骨界面结合特征与步态的作用关系,并在此基础上,建立了面向羊膝关节半髁置换的大面积骨软骨支架的设计和手术方法。
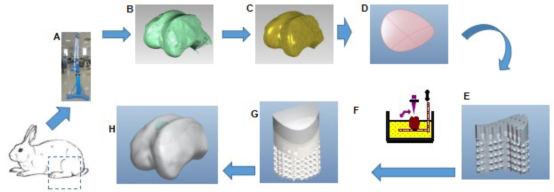
图7-1大尺寸骨/软骨支架的仿生结构设计方法
研发了多材料和多尺度结构支架精确光固化增材制造方法,已形成了大尺寸仿生支架制造的实验平台与设备。该设备以新体系光固化陶瓷浆料和打印方法为核心,建立了无分层结构的连续打印现象。目前该技术具有成形过程的缺陷自动控制策略,形成了2套完整的光固化陶瓷3D打印工艺方案与实验样机,可满足动物实验所需的大尺寸仿生支架(30mm×30mm×30mm)的快速制造和个性化结构复杂性与精度需求。
实现了同时满足骨软骨力学环境和生理环境的体外培养和评估系统,动物实验(兔、犬、羊)验证了骨软骨复合材料支架的设计制造的有效性。利用该技术,可对不同载荷等力学环境下自然关节组织的生存状态进行研究。已经初步证实力学条件对于自然关节组织的促进作用;初步建立并进行了羊股骨内侧髁大块骨软骨缺损模型动物实验及体内生物性能检测,发现通过仿生设计、生物陶瓷/水凝胶复合大块骨软骨修复体可以修复羊膝骨软骨缺损,修复性能良好。
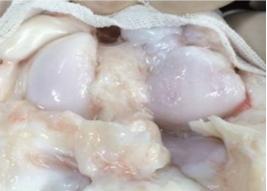
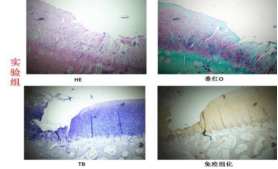
图7-2关节软骨缺损修复实验:羊股骨半髁缺损的新生软骨(左图为大体观察,右图为组织学染色)
利用该技术通过研究多材料定制化大尺寸骨/软骨支架,系统进行了相关的设计,制造,评估及动物试验方面的基础、前沿研究,为临床应用提供理论基础。
(8)可降解个性化替代物3D打印与临床应用
本项目采用可降解材料进行3D打印,以乳房修复和气管软化病为应用开展了研究工程。
乳腺癌是影响全球妇女的第一大恶性肿瘤,传统的全切手术曾对女性患者造成了严重的身体和心理的双重伤害。随着保乳手术逐渐成为女性乳腺癌患者的一种标准术式,现有的硅胶假体和自体组织填充物很难满足乳腺完美重建的功能需求。针对该问题,本项目建立了柔性可降解软组织支架仿生设计与3D打印方法体系,和第四军医大学西京医院合作,实现了国际首例的个性化可降解柔性乳腺支架的临床试验,目前已完成4例,不仅可实现初期形态与力学性能匹配,后期还可通过患者乳腺组织再生与支架降解实现自体修复,从而为乳腺癌的保乳治疗提供了新途径。
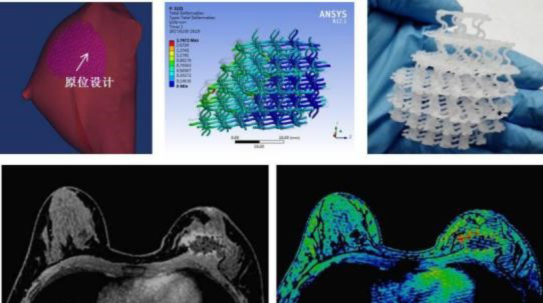
图8-1个性化可降解柔性乳腺支架的设计制造与临床应用
气管软化症是临床常见的气管疾病,其病情发展迅速、危及生命。对于较大长度(成人>6cm)的气管软化症,目前缺乏有效的治疗途径。针对该问题,和第四军医大学唐都医院胸腔外科、西京医院心血管外科以及郑州大学第一附属医院合作,利用建立的软组织支架仿生设计与3D打印方法体系,提出了基于可降解的气管外支架的气管悬吊手术方式,实现了国内首例临床试验,目前已完成临床试验研究4例(图2)。美国哈佛医学院儿童医院食管与气管中心主任RW. Jennings教授等对临床试验发表专题评论:“首次报道了3D打印气管外支架在二次气管软化成人患者的应用,展现了可行有效且安全的初期疗效”。临床应用被CCTV7、CCTV10、新华社、人民日报等专题报道,产生了良好的社会影响。
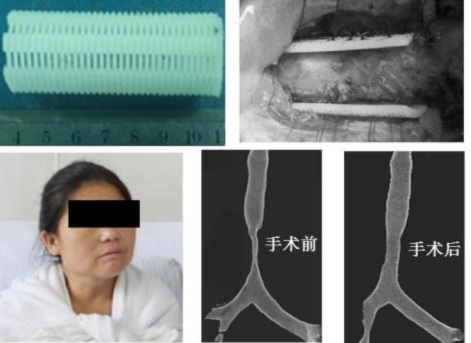
图8-2生物3D打印的气管外支架临床应用
(9)多喷头细胞3D打印技术
项目研究多细胞的在体3D打印技术,以研发血管肌肉等多组织的制备技术。本技术出以喷墨、挤压打印工艺为核心,开发多喷头生物3D打印设备,将水凝胶与细胞等活性物质根据凝胶交联特征配制生物墨水,用于人工血管/肌肉或皮肤等软组织支架的精确制造方法,为解决人工移植组织或器官的血管化和复杂结构支架制造瓶颈提供新的方案。
自制设备最大打印范围为100mm×100mm×100mm,可为裸鼠等小动物提供无菌、原位打印的手术条件。多喷头系统面向多种材料不同的成胶机理,提供了同轴喷头、喷雾喷头、单管喷头,可完成400~1200μm空心管凝胶和微丝凝胶的打印。利用多喷头运动结构和控制软件,实现多喷头间的协同工作,完成含多种材料的血管/肌肉复合组织的一体化打印。
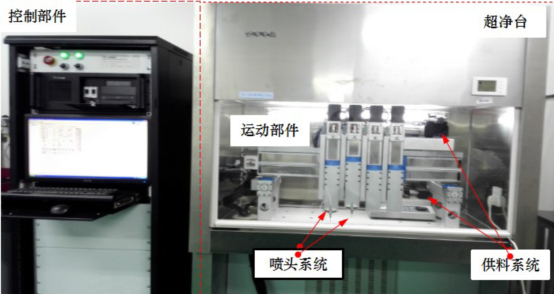
图9-1自制多喷头生物3D打印设备
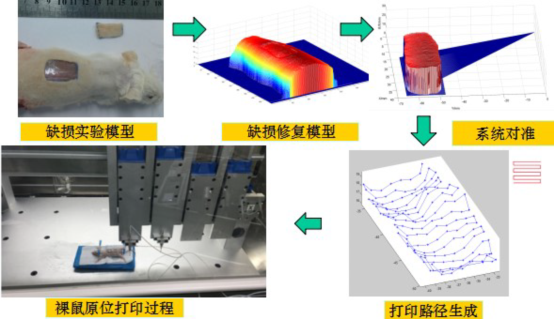
图9-2原位打印动物实验
三、技术成熟度
□概念验证□原理样机☑工程样机□中试□产业化
四、合作方式
□联合研发□技术入股□转让□授权(许可)☑面议